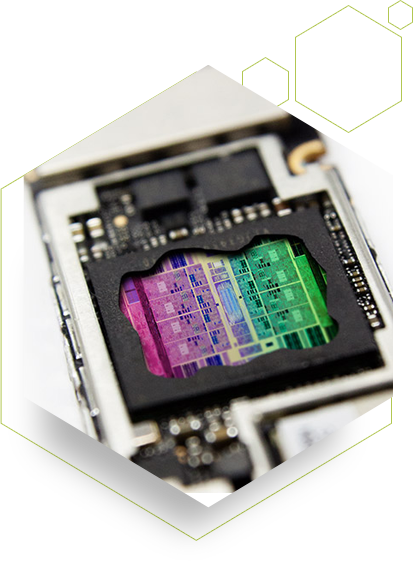
Inside every smartphone, tablet, and notebook computer
is a host of integrated circuits – the little black squares and rectangles that make up the heart, the soul, and the brain of a device. What you see is not the chip itself, but rather the black epoxy resin packaging that insulates and protects the chip inside. The chip is typically a small, thin piece of silicon containing millions of microscopic electrical components and connections.
Before these chips are packaged
and integrated into your electronic device, each one is a single die on part of a much larger piece of silicon called a wafer. Building integrated circuits on the wafer surface requires hundreds of steps, many of which involve the use of light to transfer the complex circuit patterns into a photosensitive coating. This process is called photolithography, and it is one of the most critical and challenging steps in the process of manufacturing tiny integrated circuits.
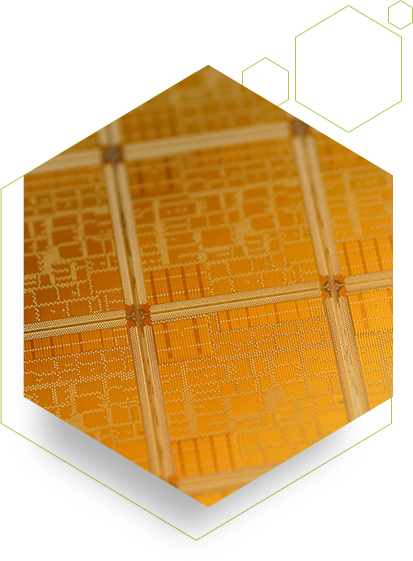
But a challenge arises…
in that silicon wafers are shiny and reflect the light used to create the microscopic circuit patterns on the surface. Chip makers had to find a way to manage the reflections that bounce off the wafer during photolithography.
That’s where we come in.
Control the light. Change the world.
Brewer Science has been developing cutting-edge materials and processes for controlling light during photolithography for over four decades. Without advances such as ARC® anti-reflective coatings, electronics would not be as small, fast, or affordable as they are today.
But we didn't stop there.
Controlling light isn’t the only way Brewer Science shines. With over 40 years of experience in materials research, we are constantly looking for new ways to move technology forward. A few other areas where we are making waves include 3-D stacking of integrated circuits and smart devices & printed electronics.